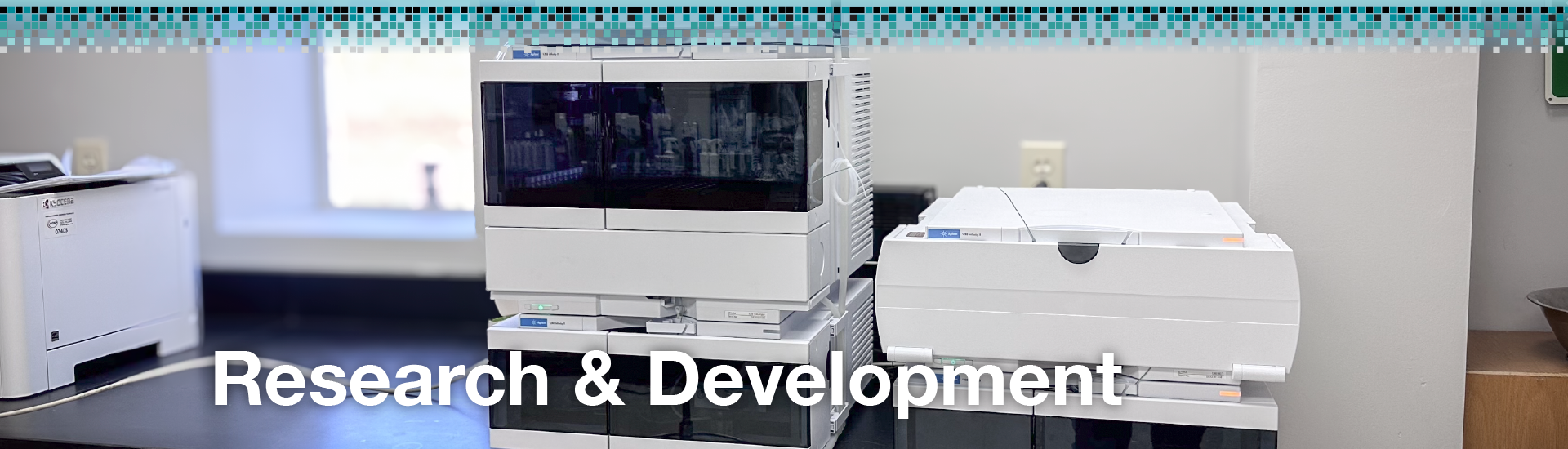
Background
Clean Control Corporation is a small but growing company focused on specialty chemical product development, manufacturing, quality control, technical service, and pesticide and chemical regulatory compliance.
Clean Control Corporation is classified in the soap and detergent trade as a compounder. That is, we do not manufacture chemical substances as defined by The Toxic Substances Control Act of 1976. Under the North American Industry Classification System (NAICS) standard, Clean Control Corporation is classified as: 325612 Polish and Other Sanitation Good Manufacturing.
Research & Development
Since incorporation in 1991, Clean Control Corporation research and development has been built upon the foundation of high performance products that meet customer expectations without harming people, property or the environment through innovation of products, processes, organization and marketing.
Product Innovation – New or significantly improved existing products.
Process Innovation – New or significantly improved practices, technologies or delivery systems.
Organizational Innovation – New or significant changes in manufacturing structure, management methods or information exchange systems.
Marketing Innovation – New or significant changes to packaging, sales methods or distribution channels.
Performance Testing
Cleaning products must meet customer expectations or customers will not use them. These expectations typically include efficient soil removal, low residue under use conditions, product stability, and package stability. Over the past 50 years, several organizations have come to be recognized in specialized areas of performance testing.
Soil Removal – Generally recognized soil removal efficiency standards have been developed by several organizations including ASTM, CSPA, and ISO.
Surface Damage – Some cleaning efficacy protocols may also include a surface damage component. For instance, a neutral floor cleaner may be tested to assure polymer floor finishes are not damaged by the cleaner at the highest recommended use dilution. In aircraft cleaners, special corrosion tests may be indicated.
Residue – In addition to ASTM, CSPA, and ISO; certain certifying organizations may develop residue (and other) test protocols. For instance Carpet and Rug Institute and The WoolSafe Organisation have developed test protocols to determine the amount of resoiling residue left on carpet after cleaning. Glass cleaners may be evaluated for filming and streaking.
Storage Stability – The “shelf life” of a product can be defined as the study of the product over time. Accurately determining a product’s shelf life is an essential part of ensuring regulatory compliance, product safety and consumer satisfaction. Typically, physical appearance, odor, viscosity, microbial challenge and active ingredient concentration are studied.
Package Stability– Typically containers are exposed to extreme conditions and ambient for prolonged periods of time to determine effects of temperature and chemicals on package strength and integrity.
Internal Testing – Standard internal testing protocols based on ASTM and nationally recognized standards are established determine if products perform to a minimum expectation.
Independent Testing – Independent testing is performed to validate internal protocols and when required by customers, independent auditors and regulatory compliance.
Clean Control Corporation research and development has adopted a chemical substance policy that incorporates chemical information review, regulatory oversight, and support for green chemistry research and development. Chemical substances used for compounding are screened for human and environmental attributes. Only the safest substances in a class are considered for product development.
Research & development in the cleaning industry is a complex process that requires specific technical, communication and regulatory skills. Technical skills include organic chemistry, analytical chemistry, applied surfactant chemistry, green chemistry, applied microbiology, engineering, human and aquatic toxicology, industrial hygiene and computer technology. Communication skills include organizational, recordkeeping, problem solving; as well as, technical writing and verbal. Regulatory skills include OSHA, EPA, FIFRA, DOT, CPSC, FDA, Good Manufacturing Practice (GMP) and Good Laboratory Practice (GLP).
Health & Safety
Cleaning products must be used safely and any hazards must be identified. During product development, Research & Development works closely with Graphics, Technical Service, Information Technology, Customer Service, Risk Management, Operations and Quality Control to ensure employees and end-users; as well as, transportation and distribution partners receive information regarding those hazards. Information regarding industrial and institutional cleaning products; in the form of labeling and Safety Data Sheets, is regulated in the United States by the Occupational Safety and Health Administration. Other information required by national and state standards may also be included. Additionally, process safety procedures must be developed to prevent unintentional worst-case-scenario hazards from occurring during manufacturing; spill response plans and training must be implemented.
Safety Data Sheets – SDSs include information such as: Product Identification, hazardous ingredients, first aid, fire and emergency procedures, handling and storage, personal protective equipment, physical and chemical properties, stability and reactivity, toxicological, ecological, transportation, disposal and regulatory information.
Labels – Labels include product Identification, hazardous ingredients, first aid, how to dilute, use, store and handle.
Customer Service Database – Customer Service maintains a database of customer calls, problem index of all calls. Research & Development reviews all calls for adverse effects and classifies them for use in updates, notifications and regulatory reporting.
Environment and Sustainability
Products developed that perform as expected and are safe to use in the traditional sense, may still present an environmental burden on indoor air quality, wastewater discharges and eventually aquatic environments. Research and Development into products that are more environmentally sustainable requires additional emphasis on substitution of traditional ingredients with ingredients that are less harmful, biodegradable and which degrade readily into non-polluting products. For additional information see sustainability.
Communication
During product development, processes and procedures must be in place to assure that every aspect of customer and regulatory compliance is accounted for.
Interdepartmental – Internally, each department plays an integral and interrelated role.
Sales & Marketing, Graphics, Technical Service, Information Technology, Customer Service, Purchasing, Risk Management, Quality Control and Operations
External – Communications with third party verifiers play a key role in verification of procedures and review of records. These verifiers include: Regulatory audits, Independent audits, Consultants, NGOs and Trade Organizations
Training
As a small family-owned business, we recognized to value of working closely with our partners, providing assistance with numerous issues, including training in the use of our products. Training is conducted onsite and through regular updates of our labeling, product information and website (odobanprofessional.com).
During product development, Research & Development works closely with Graphics, Technical Service, Information Technology, Customer Service and Sales & Marketing to develop product information for use by our partners and distributors on the proper use of the product (instructions on how to dilute, use and dispose of the product, handling and other worker safety information).
Quality Control
Research & Development works closely with the Quality Control Department to establish a system which:
- Documents quality control testing protocols, analytical methods and procedures
- Facilitates corrective action when necessary
- Maintains a database of information to conduct
- Internal and Independent Quality Audits
- Customer Inspections
- Government Inspections
- Product Safety Recalls
- Promotes distributor and end-user confidence and satisfaction
- Protects the assets of Clean Control Corporation and customers
Verification procedures may include such activities as review of plans, records, critical limits, and microbial sampling and analysis; and include verification tasks to be performed by plant personnel. Verification tasks are also be performed by independent, Federal and state inspectors.
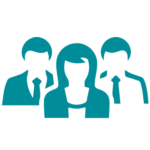